Proceso de Anodizado: ¿Cómo se anodiza el aluminio?
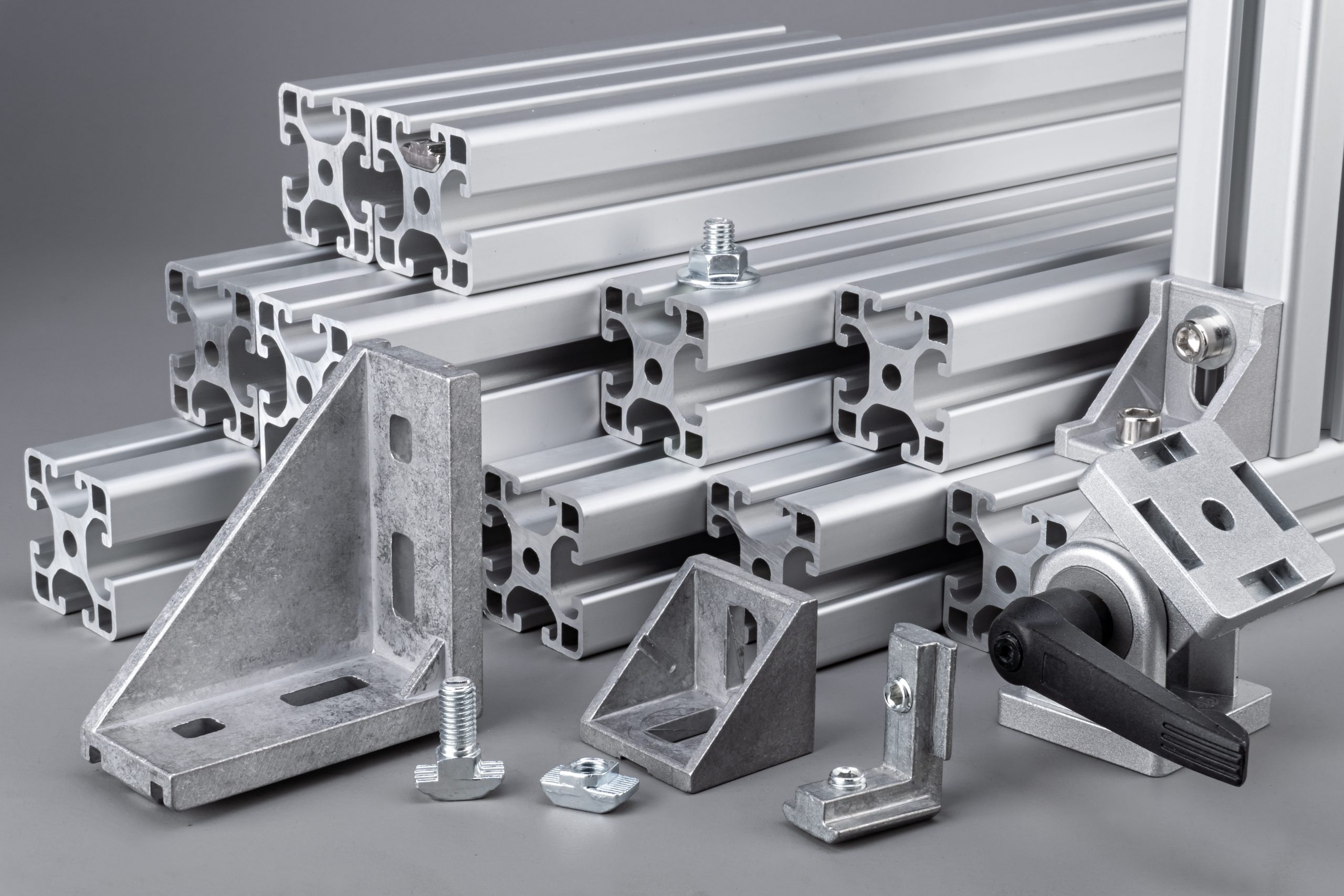
Cómo se anodiza el aluminio es una pregunta clave para muchas industrias que buscan prolongar la vida útil de este material, mejorar su resistencia y ofrecer acabados estéticamente atractivos. Sin un tratamiento adecuado, el aluminio queda expuesto a la corrosión y el desgaste, afectando la calidad y durabilidad de los productos.
Por ello, este tratamiento es muy útil en aplicaciones que requieren durabilidad, como en componentes estructurales, fachadas o piezas sometidas a condiciones extremas.
Además, también te permite personalizarlos con colores y texturas, convirtiéndolo en una apuesta segura para fines estéticos. En este artículo, te explicaremos detalladamente el proceso de anodizado del aluminio, los tipos de anodización disponibles y las opciones de acabado que mejoran tanto el rendimiento como la apariencia de tus productos.
¿Para qué sirve anodizar el aluminio?
El anodizado del aluminio es un proceso crucial para aumentar la durabilidad y resistencia del material frente a factores externos como la corrosión, el desgaste y la exposición a agentes químicos. Este tratamiento electroquímico crea una capa protectora de óxido de aluminio en la superficie, prolongando su vida útil y mejorando mejora su rendimiento en aplicaciones industriales críticas, como la construcción y la automoción.
Asimismo, el anodizado mejora la adherencia de recubrimientos adicionales, como pinturas y adhesivos, permitiendo personalizar la apariencia del aluminio sin comprometer su funcionalidad.
Este proceso también es esencial en industrias como la aeroespacial, donde el peso ligero y la alta resistencia son requisitos imprescindibles para componentes clave.
¿Cómo se anodiza el aluminio?
Como hemos mencionado, el anodizado del aluminio es un proceso electroquímico diseñado para mejorar la resistencia y durabilidad de este metal. A continuación, te explicamos cómo se anodiza el aluminio, dividiendo el proceso en tres etapas clave: preparación, anodizado y sellado.
1. Preparación de la superficie
Antes de iniciar el anodizado, es necesario limpiar el aluminio a fondo para eliminar impurezas como aceites, grasa o polvo. Este paso es esencial, ya que cualquier contaminante en la superficie podría afectar la formación uniforme de la capa de óxido.
Dependiendo del proyecto, se utilizan diferentes métodos, como la limpieza alcalina o ácida, junto con un desengrase para garantizar que la superficie esté completamente libre de residuos. Además, se puede realizar un tratamiento mecánico para nivelar la superficie del aluminio, eliminando arañazos o defectos previos.
2. Proceso de anodizado
Una vez que el aluminio está limpio, se sumerge en un baño de electrolito ácido, generalmente ácido sulfúrico o ácido crómico, dependiendo del tipo de anodizado que se vaya a realizar. Aquí, el aluminio actúa como ánodo en un circuito eléctrico, mientras que una corriente eléctrica fluye a través del electrolito, promoviendo la formación de una capa de óxido en la superficie del metal.
Esta capa no solo cubre la superficie, sino que también penetra en ella, lo que aumenta la resistencia del aluminio a la corrosión y el desgaste. El grosor de la capa de óxido varía según el tipo de ácido y la duración del proceso.
3. Sellado
Una vez completado el anodizado, el aluminio pasa por un proceso de sellado. Este paso es crucial para cerrar los poros de la capa de óxido y mejorar aún más la resistencia del material. Generalmente, se sumerge el aluminio anodizado en agua caliente o en productos químicos específicos que sellan la superficie, impidiendo la entrada de agentes corrosivos y aumentando su durabilidad.
Los tipos de anodización
Ya conoces cómo se anodiza el aluminio, pero este proceso no sigue una única metodología. Existen varios tipos de anodización, cada uno con características y aplicaciones específicas, adaptándose a diferentes necesidades industriales y estéticas.
Anodizado con ácido crómico (Tipo I)
El anodizado con ácido crómico, conocido como Tipo I, es ideal cuando se requieren capas finas de óxido, generalmente de entre 0.5 a 1 micras. Este tipo de anodización es especialmente utilizado en la industria aeroespacial, ya que genera una capa protectora delgada. Esto permite mantener la ligereza y la resistencia del aluminio sin comprometer su rendimiento.
Además, el ácido crómico tiende a crear una capa menos porosa, ofreciendo una mayor resistencia a la corrosión. Sin embargo, el rango de colores es limitado. Normalmente en tonos grises, algo que restringe su aplicación a productos donde la estética no es una prioridad.
Anodizado con ácido sulfúrico (Tipo II)
El anodizado con ácido sulfúrico, también llamado Tipo II, es el método más comúnmente utilizado en la industria debido a su versatilidad y capacidad de crear una capa de óxido más gruesa, generalmente entre 5 a 25 micras.
Esta opción es ideal para aplicaciones donde se requiere resistencia a la corrosión y al desgaste. Además, ofrece una amplia gama de opciones estéticas gracias a su capacidad para absorber tintes y lograr colores personalizados.
Por este motivo, se utiliza en productos como:
- Carcasas electrónicas
- Productos cosméticos.
- Utensilios de cocina.
- Fachadas de edificios.
Asimismo, el anodizado con ácido sulfúrico es más económico que el de ácido crómico, convirtiéndolo en una opción atractiva para muchas industrias.
Anodizado de recubrimiento duro (Tipo III)
El anodizado de adonizado duro del aluminio o Tipo III se utiliza cuando se necesitan capas de óxido de mayor grosor y resistencia, que pueden alcanzar hasta 50 micras o más. Es el más robusto y está diseñado para productos que enfrentan condiciones extremas de desgaste y corrosión, como piezas de maquinaria industrial, cilindros hidráulicos o componentes militares.
Aunque las opciones de color son más limitadas, este tipo de anodizado es clave en aplicaciones donde la funcionalidad y la durabilidad son la máxima prioridad.
Como ves, cada uno de estos tipos de anodización ofrece soluciones únicas adaptadas a las necesidades de diversas industrias. En todos los casos, el proceso asegura una protección y un acabado estético acorde con los requisitos de cada proyecto.
Los colores disponibles en aluminio anodizado
Gracias al proceso de anodizado, se pueden obtener colores como el negro, dorado, rojo, azul y verde, entre otros, aplicando tintes específicos durante el tratamiento. Además, algunos procesos de anodización pueden lograr colores más oscuros y tonos metálicos, como bronce, a través de técnicas de coloración integra.
¿Qué tipos de aluminio se pueden anodizar?
El proceso de anodizado del aluminio es compatible con varias series de aleaciones, pero las más utilizadas son las series 5XXX, 6XXX y 7XXX, debido a su capacidad para formar capas de óxido densas y uniformes.
- Serie 5XXX: Contienen magnesio como principal elemento de aleación y son reconocidas por su alta resistencia a la corrosión, lo que las hace ideales para aplicaciones marinas y estructuras expuestas a la intemperie. Son perfectas para anodizado, ofreciendo acabados duraderos.
- Serie 6XXX: Es la más versátil. Incluye aleaciones de aluminio con magnesio y silicio. Se utiliza en la construcción de estructuras, perfiles y componentes automotrices, gracias a su equilibrio entre resistencia mecánica y facilidad de anodizado.
- Serie 7XXX: Ricas en zinc, son muy utilizadas en la industria aeroespacial debido a su altísima resistencia mecánica. Aunque su anodizado puede ser más complejo, el resultado es una capa de óxido extremadamente resistente, ideal para entornos exigentes.
Ahora que ya comprendes cómo se anodiza el aluminio, es el momento de apostar por un enfoque que se adapte a las necesidades específicas de tu sector. Como ves, la anodización es un proceso que optimiza la funcionalidad del aluminio y ofrece acabados estéticos personalizados, ideales para proyectos que demandan alta calidad y rendimiento.
Si buscas asegurar calidad y precisión en tus productos, trabajar con especialistas en anodizado es el primer paso para lograr resultados óptimos y sostenibles. ¡Contáctanos y mejora tus proyectos con los productos que necesitas!